What is an environmental test chamber?
Sue James • May 6, 2020
For an environmental test chamber engineer, the answer to an opening line of “What do you do?” can provoke one of two outcomes: curiosity - or a slightly glazed look and a wish of having never asked!
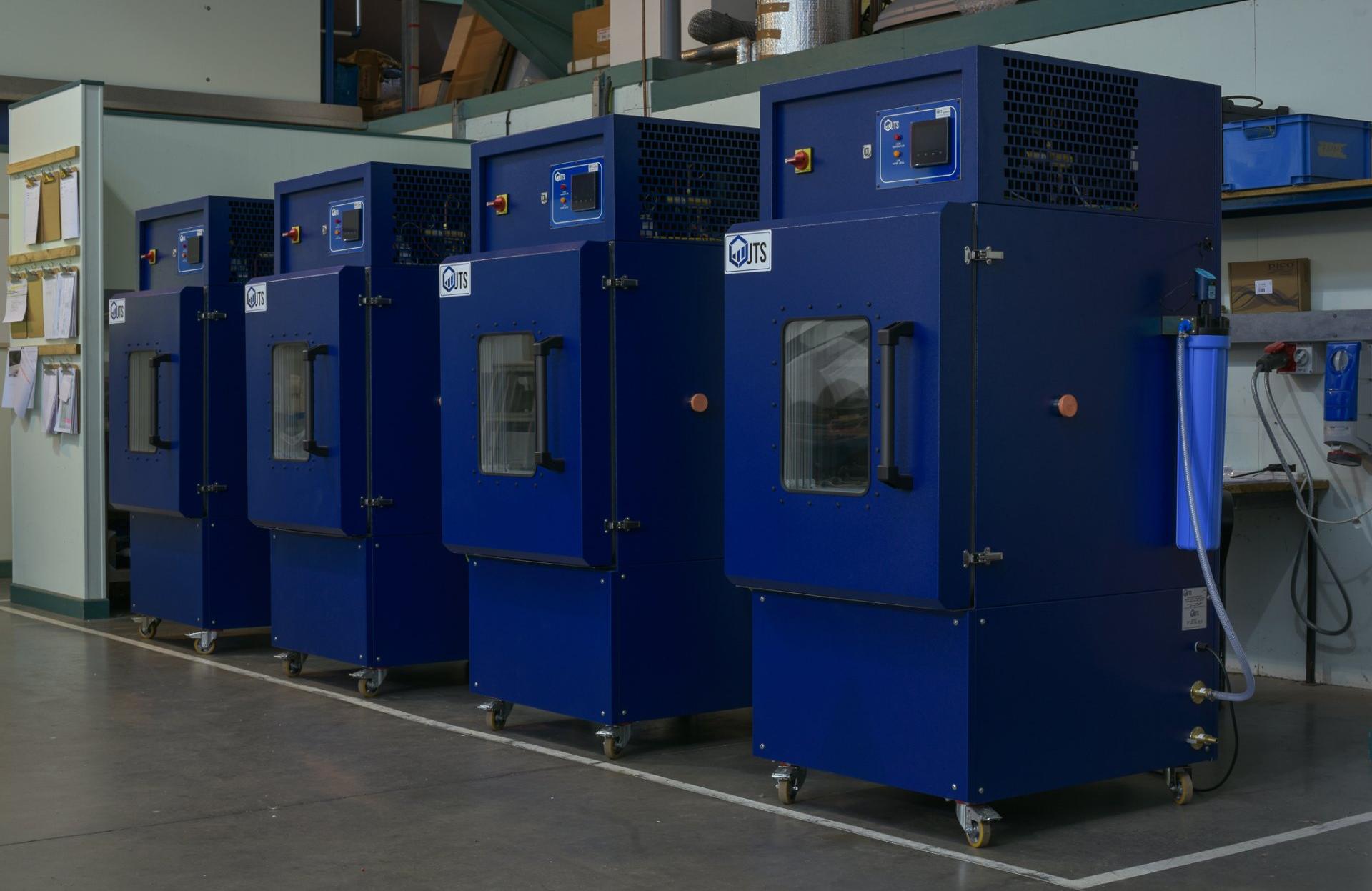
So, what is an environmental test chamber? In this short series we’ll introduce you to the how’s and why’s.
The simplest way to explain what a test chamber is, is to describe it as a highly insulated cupboard, fitted with various systems to simulate environmental conditions eg refrigeration for cold and humidity for damp. It can be small enough to fit on a bench – or big enough to hold a car or two. They are used to research, develop and manufacture many of the products in everyday use.
The chamber has a controller and can be programmed to give different cycles through hot and cold, dry and humid, even rain or dust or salt spray, according to requirements and specifications. The tests can also ensure adherence to certain Standards for products.
The test results help predict the potential lifespan of a product or material, and how well it will stand up to the conditions it will be expected to operate in. Test chambers can also be used to evaluate product quality and reliability, and to identify manufacturing weaknesses.
Examples of the products our test chambers have been used for:
• Deep sea pipeline valves (operation at cold temperatures);
• Traffic light sensors (need to be operational in all weathers);
• Office equipment (testing laminated materials);
• Electronic devices (how well will your phone operate in the rain…?);
• Smoke detectors, fire alarms & toxic gas detectors;
• Aerospace components (taking off in a hot desert, going up into cold atmosphere).
Click here to find out more about our test chambers, or call us if you have a requirement you’d like to discuss.
Next up: Inside a Test Chamber: how it works...
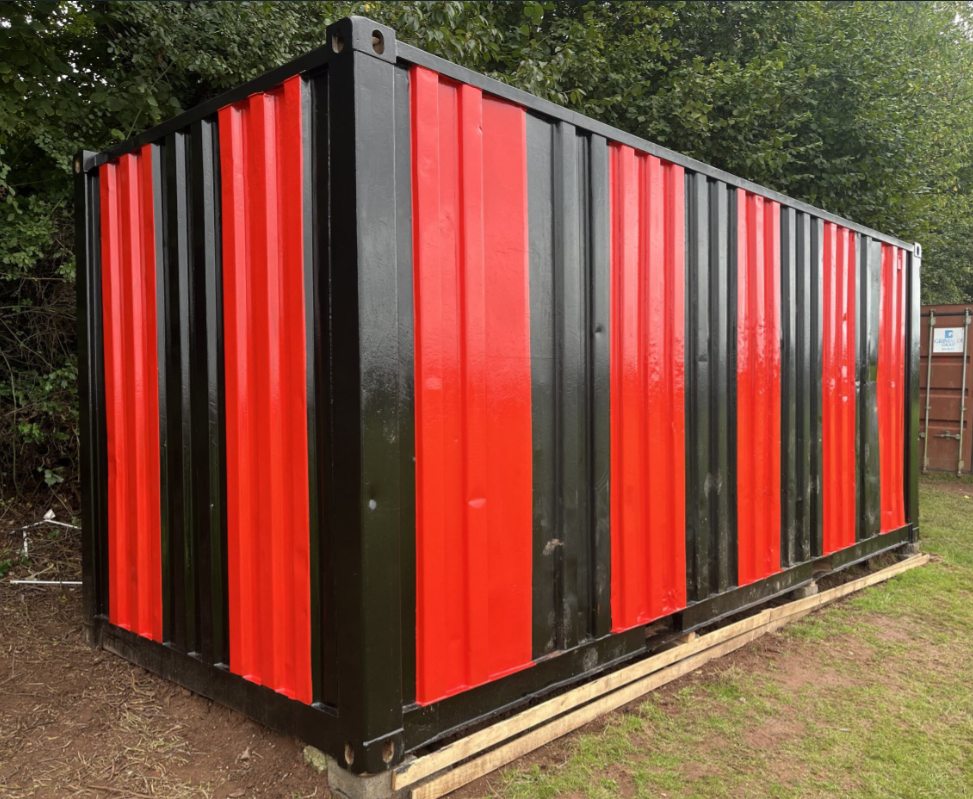
JTS were asked by local councillor William Powell to help out refreshing a storage container used by Talgarth Town FC juniors and ladies. After some initial discussions and a quick cad mock up to agree the paint scheme the JTS team began to work on the project. This happened with the help of the Black Mountains College (Power) and Talgarth Building Supplies (Paint) and the JTS workforce. As you can see the container has had a new lease of life and we hope the guys using the container like the paint work! ‘Good news TTFC under 10’s celebrated a home victory with the team having a photo and the container used as a back drop!’
James Technical Services Limited having been involved in electric car, battery development and testing over the past 7 years have now installed two 11kW charging points at the factory in Talgarth mid Wales. These points can be used by customers and employees 😊 JTS have always been following the progress of the battery development and have purchased their first electric vehicle which will be used by the employees to carry out sales / site visits. The container test chamber below is used by various car manufacturers for electric vehicle battery testing. This is just one example of a battery testing facility JTS can supply.